Call us today!
Blog
Woven Geotextile vs Non Woven Geotextile
The primary difference between ‘non woven geotextile’ and ‘woven geotextile’ lies in their manufacturing process, structure, and resulting properties, which are both widely used in road construction,drainage systems,landfill and all kinds of civil engineering.But they differ in their manufacturing processes, properties, and applications.
1. Manufacturing Process & Structures
– Made by weaving continuous synthetic fibers (usually polypropylene or polyester) into a fabric using traditional weaving techniques.
– Produces a strong, uniform, and stable fabric with high tensile strength.
– The fibers are arranged in a specific pattern (plain weave or twill weave) to create a more structured and uniform material
– Made by bonding synthetic fibers together mechanically (needle-punching), thermally, or chemically.
– Results in a felt-like, porous fabric with higher permeability.
– The fibers are randomly oriented, creating a web-like structure.
2.Physical Properties
– Thinner and less porous.
– Lower permeability, making them less effective for drainage or filtration.
– Higher tensile strength, especially in the direction of the weave.
– More resistant to punctures and abrasion.
– Thicker and more porous.
– Higher permeability, allowing water to pass through easily.
– Lower tensile strength compared to woven geotextiles but still strong enough for many applications.
– Better at separating and filtering materials.
3. Applications
– Road stabilization (subgrade reinforcement)
– Embankment support
– Erosion control in slopes
– Primarily used for reinforcement and stabilization purposes.
– Roadways, railways, embankments, and retaining walls to increase load-bearing capacity and prevent soil movement.
– Suitable for applications requiring high tensile strength and durability.
– Drainage systems (behind retaining walls, under roads)
– Landfill liners and leachate collection
– Protection for geomembranes
– Soil filtration in silt fences
– It is used for separation, filtration, and drainage applications.
– Ideal for road construction (base stabilization), erosion control, landfill liners, and subsurface drainage systems.
– Suitable for environments requiring high permeability and flexibility.
4.Cost & Durability
Woven geotextiles are generally more durable under heavy loads but can be more expensive
– More resistant to UV degradation and chemical exposure.
– Longer lifespan in demanding conditions, especially in reinforcement applications
– More expensive due to the weaving process and higher tensile strength.
– Justified in applications requiring strong reinforcement.
Non woven geotextiles are cost-effective for filtration and drainage but may degrade faster under UV exposure if not stabilized
– More susceptible to UV degradation and chemical exposure over time.
– Typically have a shorter lifespan compared to woven geotextiles in harsh environments.
– Generally less expensive than woven geotextiles.
– Cost-effective for applications where high tensile strength is not critical.
5.Summary
Woven Geotextile (high-strength applications like reinforcement)
-Manufacturing:Woven fibers (plain or twill weave)
-Permeability:Low
-Tensile Strength:High
– Puncture Resistance:High
-Filtration:Poor
-Separation:Good
-Applications:Reinforcement, stabilization
-Durability:More resistant to UV/chemicals
-Cost:Higher
Non Woven Geotextile (drainage, filtration, and separation needs)
-Manufacturing:Bonded fibers (needle-punched, thermal)
-Permeability:High
-Tensile Strength: Moderate
-Puncture Resistance:Low
-Filtration:Excellent
-Separation:Excellent
-Applications:Separation, filtration, drainage
-Durability:Less resistant to UV/chemicals
-Cost:Lower
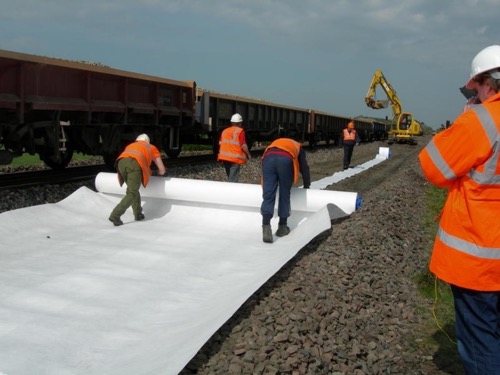
Keywords:
PET Non Woven Geotextile